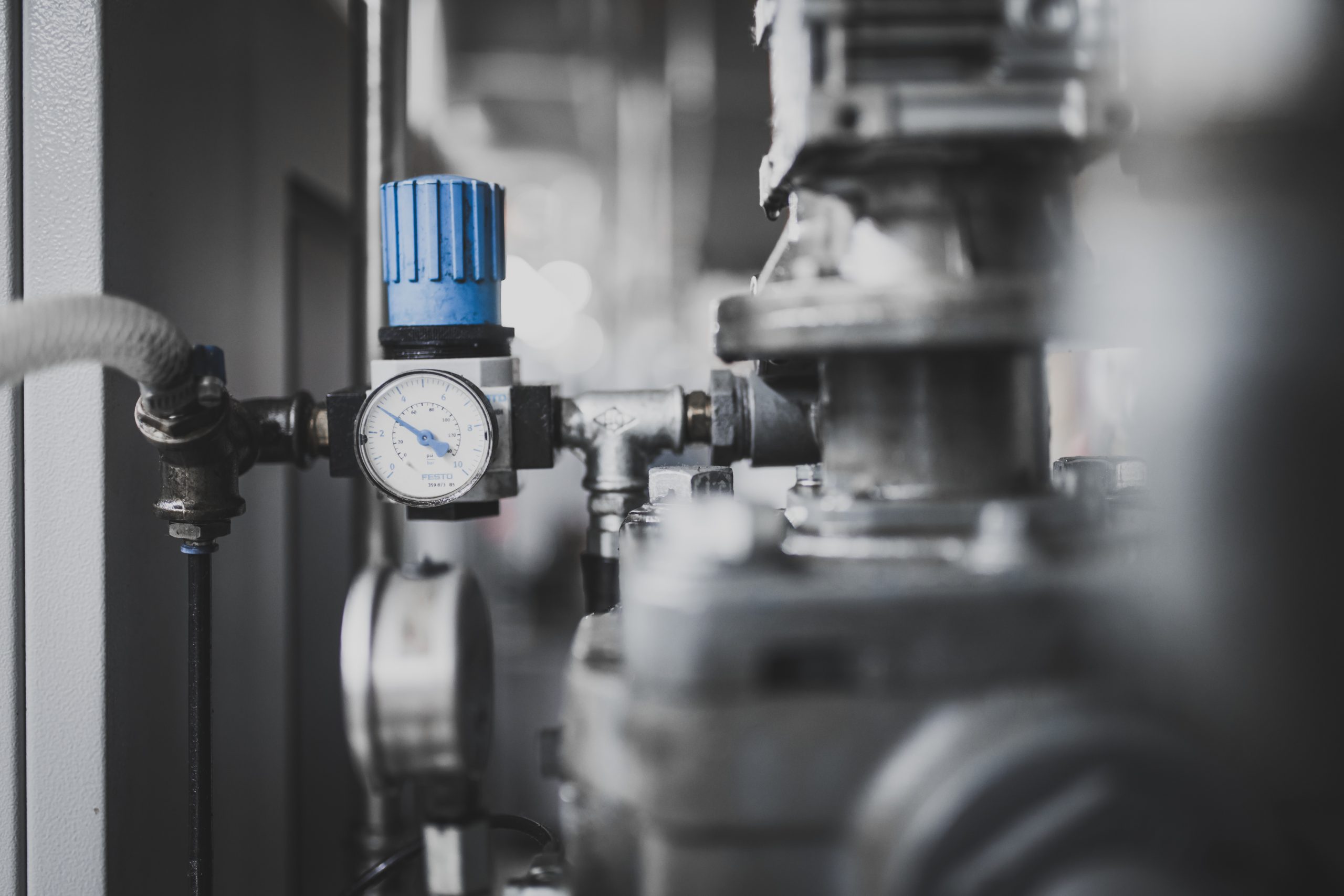
Wie funktioniert Hydraulik? Prinzip und Funktionsweise
Ehe wir hier auf die Frage „Wie funktioniert Hydraulik?“ und die Funktionsweise beim Hydraulikmotor näher eingehen, wollen wir mal einen Blick auf die Definition werfen.
Der Begriff Hydraulik stammt aus dem Altgriechischen und beinhaltet die Worte hýdor, gleich „Wasser“, sowie aulós, das „Rohr“. Bei der Hydraulik und ihrer Funktion haben wir es also mit Leitungen, beziehungsweise Rohrsystemen zu tun, in denen Wasser oder andere Flüssigkeiten einen Druck aufbauen.
Hydraulik-Funktion – wie man sich diese vorstellen kann
Um zu begreifen, wie eine Hydraulikpumpe oder auch die Hydraulik selbst funktioniert, können wir daher auf eine medizinische Apparatur schauen, das im Zuge von Impfungen oder nach Behandlungen den meisten von uns bekannt ist, nämlich eine Spritze.
Auch hier befindet sich eine Flüssigkeit, in diesem Fall ein Arzneimittel oder ein Impfstoff, in einem Kolben und wird durch Druck auf der einen Seite in Richtung der Injektionsnadel bewegt und von dort weiter in den Organismus gepresst.
Vereinfacht ausgedrückt, geht es bei der Hydraulikmotor-Funktion und der Frage „Wie funktioniert Hydraulik?“ also um das Strömen von Flüssigkeiten in Kolben oder auch Rohr- und Schlauchsystemen, und darum, wie sich mittels Druck auf diesen Flüssigkeiten Lasten bewegen lassen. Die meisten Hydrauliksysteme setzen heutzutage auf Hydraulik Drehteile, wie zum Beispiel Hohlschrauben.
Wie funktioniert Hydraulik und wo kommt diese zum Einsatz?
Doch lasst uns die Frage „Wie funktioniert Hydraulik?“ am besten einmal an ein paar konkreten Beispielen festmachen: Hydraulik, die Lehre von der Kraft strömender Flüssigkeiten, wird in Baumaschinen, Baggern und Hebebühnen benutzt.
Auch Aufzüge oder das Fahrwerk von Flugzeugen arbeiten hydraulisch. Für Ingenieure gehört daher das Wissen um die Frage „Wie funktioniert Hydraulik?“ quasi zum kleinen Einmaleins. Hier sind Pneumatik und Hydraulik gang und gäbe.
Vereinfacht ausgedrückt, erzeugen Druck sowie die daraus resultierende Bewegung eines Hydrauliköls eine Energie, die wir für diverse Zwecke nutzen können. Zum Beispiel, um Lasten scheinbar spielend leicht zu bewegen. Dabei werden die genutzten Systeme mittlerweile immer umweltfreundlicher, zum Beispiel können Mineralöle in Hydraulikmotoren heute häufig auch durch Wasser oder Glykole ersetzt werden.
Es geht für Konstrukteure also nicht nur um die Frage „Wie funktioniert Hydraulik?“, sondern auch darum, Motoren so nachhaltig wie möglich zu gestalten, damit diese auch in Zukunft genutzt werden können, ohne die Umwelt unnötig zu belasten.
Hydraulik-Funktion: Signal-, Kraft- und Energieübertragung
Das Wissen darum, wie Hydraulik funktioniert und eingesetzt werden kann, ist also ein spannendes Feld. So gut wie jeder Mensch kommt in seinen Alltag mit verschiedenen Technologien in Kontakt, die zumindest in Teilen hydraulisch angetrieben werden, wie zum Beispiel im Auto oder im öffentlichen Nahverkehr. Denn nicht nur die Lenkung von Fahrzeugen sondern auch die Bremsen setzen auf das Prinzip der Hydraulik. Im Kontext von Fahrzeugen wird dabei ein oft schnell bewegendes, tonnenschweres Gefährt mittels eines vergleichsweise leichten Drucks auf ein Pedal abgebremst.
Wie funktioniert Hydraulik und wo liegen dessen Vorteile?
Tatsächlich zeichnen sich gerade hydraulische Motoren durch ihre lange Lebensdauer aus. Denn die benutzte Flüssigkeit ist zugleich Korrosionsschutz (außer beim Einsatz von Wasser) wie auch Kühlmedium.
Zudem lässt sich die im Betrieb auftretende Belastung durch Druckmessgeräte einfach ablesen und – falls nötig – via Druckbegrenzungsventil regulieren.
Vor allem jedoch lassen sich mit dem Wissen „Wie funktioniert Hydraulik?“ große Kräfte und Drehmomente äußerst einfach aufbauen.
Wie funktioniert Hydraulik und was sind dessen Schwächen?
Allerdings müssen hinsichtlich der Frage „Wie funktioniert Hydraulik?“ auch die Nachteile benannt werden, die mit hydraulischen Systemen verknüpft sind. Denn Leckagen und Ölverluste führen in dem in sich geschlossenen System rasch zur Leistungsminderung und schließlich zu einem kompletten Stillstand.
Für die Frage, wie und ob Hydraulik funktioniert, ist zudem die Umgebungstemperatur von Belang. So werden viele der in hydraulischen Systemen benutzten Flüssigkeiten bei Minusgraden immer zähflüssiger, was zur Erhöhung der inneren Reibung führt; die Energie nimmt dabei ab.
Auch die Geräuschentwicklung allgemein sowie die Schaltgeräusche der verbauten Ventile müssen zu den Nachteilen dieser Form der Kraftgewinnung gezählt werden. Dennoch sind Hydraulikschrauber oder auch Gabelstapler sowie Forstgeräte mit hydraulischen Arbeitsantrieben heute unverzichtbare Helfer im Arbeitsalltag und das Produkt findiger Köpfe, die sich mit der Frage, wie Hydraulik funktioniert und wie sie sich für uns Menschen nutzbar machen lässt, auseinandergesetzt haben.
Wie funktioniert Hydraulik? Joseph Bramah ging der Frage damals auf den Grund
Als einer der großen Begründer der technischen Hydraulik gilt der Engländer Joseph Bramah. Aber auch William George Armstrong, ein waschechter Baron und britischer Industrieller, hat sich mit der Frage „Wie funktioniert Hydraulik?“ und mit der Frage, wie sich dieses Wissen für Motoren oder Hebebühnen nutzbar machen lässt, intensiv befasst.
Die sogenannte Ölhydraulik begann im Jahre 1905, während Bramahs Gerätschaften 1795 noch mit Druckwasser betrieben wurden.
Heute zählt die Frage „Wie funktioniert Hydraulik“ längst zum technischen Allgemeinwissen und ist jedem Ingenieur bekannt. Mittlerweile kommt diese in den verschiedensten Branchen und Maschinen zum Einsatz, zu den bekanntesten Anwendungsgebieten zählen dabei hydraulische Getriebe und Hubbühnen. Aber auch Panzer und Fregatten sowie Gleisbremsen auf Rangierbahnhöfen bedienen sich der Hydraulik.