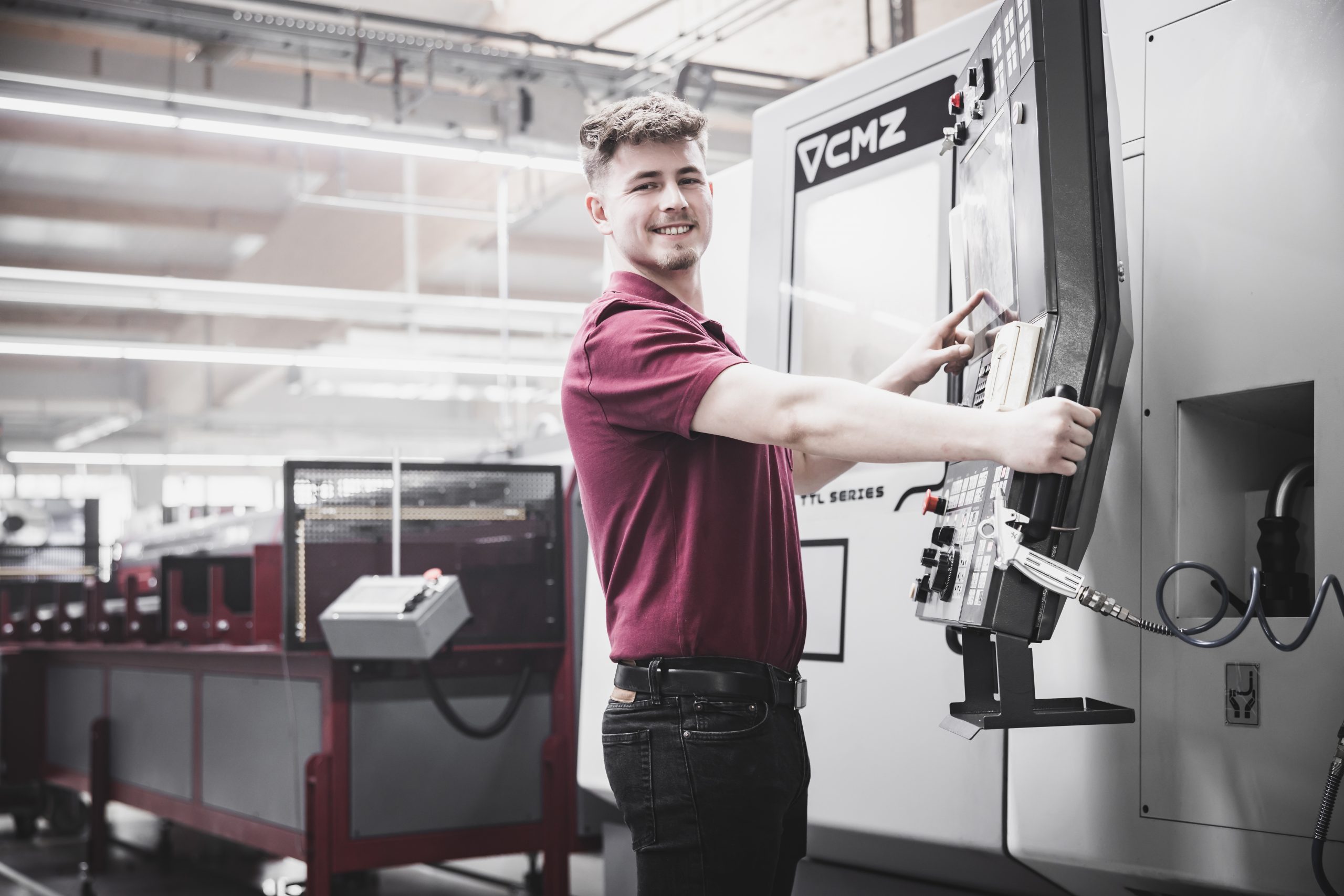
Nachhaltige Produktion – Gemeinsam für die Umwelt
Niemand weiß genau, was in der Zukunft passiert. Gerade in der aktuellen Zeit ist die Zukunft sehr ungewiss, da Naturkatastrophen durch den Klimawandel die gesamte Situation auf der Welt verändert haben. Menschen haben reale Ängste um ihre Zukunft und über die Zukunft ihrer Kinder und Enkel.
Doch eigentlich stimmt die erste Aussage nicht ganz, dass „niemand genau weiß, was in der Zukunft passiert“, da Experten bereits vor vielen Jahrzehnten von den katastrophalen Auswirkungen der Klimaveränderung berichtet hatten. Selbst in der jetzigen Zeit, in der der Klimawandel real und einige Folgen bereits bekannt sind, versuchen viele diesen Faktor zu verdrängen.
Glücklicherweise sieht nur ein kleiner Teil der Menschheit den Klimawandel nicht ein, weshalb sich viele Menschen inzwischen für eine umweltschonende Politik einsetzen und ihr Bestes versuchen, um Ihrer Umwelt Gutes zu tun. Die aktuelle Frage bleibt aber, ob die jetzigen Maßnahmen ausreichen, um fatale Folgen zu vermeiden. Es wurde zwar bereits gesagt, dass einige Veränderungen sicherlich eintreffen und dass es womöglich auch Klimaflüchtlinge geben wird, aber die genauen Folgen sind noch unbekannt und liegen in der Hand der Menschheit.
Dazu kann jeder Mensch etwas beitragen, sei es nur die Vermeidung von Plastiktüten oder die korrekte Entsorgung von Müll. „Kleinvieh macht auch Mist“ und dies gilt selbstverständlich auch für den Klimawandel und eine nachhaltige Produktion. Wenn jeder anpackt, die eigene Situation verbessert und umweltfreundlicher wird, dann hat die Erde gute Perspektiven vor sich.
Doch einzelne Menschen können nicht allein über die Zukunft entscheiden und benötigen das Einverständnis von mächtigen Personen. Dazu gehören die Menschen, die in Machtpositionen in der Politik sitzen. In Deutschland bemüht sich aktuell vor allem die Partei „Bündnis 90 – Die Grünen“ um eine umweltbewusste Politik.
Gleichzeitig nutzen sie ihre aktuelle Position aus, um noch mehr Werbung gegen den Klimawandel und den Menschen deutlich zu machen. Zudem appellieren sie auch an Unternehmen, die möglichst eine nachhaltige Produktion anstreben sollen, da sie eine zentrale Rolle im gesamten Klimawandel spielen.
Nachhaltige Produktion – Unternehmen Loga
Drehteile Loga setzt sich bereits seit der Gründung für eine nachhaltige Produktion ein, was inzwischen über 30 Jahre her ist. Bereits damals machten wir uns Gedanken darüber und implementierten ein umweltschonendes Konzept in unser Unternehmen. Natürlich haben wir seither vieles gelernt und uns deutlich weiterentwickelt.
Inzwischen gehören wir zu den Spezialisten für Drehteile und arbeiten komplett mit einer nachhaltigen Produktion in unserem Unternehmen. Dabei legen wir nicht nur Wert darauf, dass wir wenige Teile oder Materialien verschwenden, sondern auch sehr wenig CO2 erzeugen. Zusätzlich setzen sich unsere Mitarbeiter dafür ein, dass sie umweltbewusst handeln und Experten auf diesem Fachgebiet sind.
All ihre Entscheidungen werden mit dem Hintergedanken zur Umwelt getroffen und diesen Leitgedanken teilen sie mit ihren Mitmenschen. Unser Ziel ist es, dass die Umwelt möglichst wenig, besser gar keine Schäden durch unsere Produktion erleidet. Dieser Gedanke wird sehr von unseren Mitarbeitern und Kunden wertgeschätzt, da sie genau wissen, wie wichtig dieses Thema aktuell und für die Zukunft ist.
Zudem sind wir stolz darauf, dass wir vom ICG-Institut für unsere nachhaltige Produktion ausgezeichnet wurden und sehen diese Auszeichnung als Ansporn. Obwohl unser primäres Ziel selbstverständlich nicht der Klimawandel ist, setzen wir diesen Faktor dennoch mit unserer Produktion für Drehteile gleich.
Nachhaltige Produktion – Blick auf die Zukunft
Früher oder später wird es in Deutschland Pflicht sein, dass nur gewisse Mengen an CO2 bei der Herstellung entstehen dürfen. Deshalb sind wir froh darüber, dass wir bereits seit Anfangszeiten an solch einem Konzept festgehalten haben. Umweltschutz und nachhaltige Produktion sind in der Theorie einfach umzusetzen, wenn bereits früh damit angefangen wird.
Das Erlernen funktioniert zwar auch zu einem späteren Zeitpunkt, aber prinzipiell kann es mit dem Erlernen einer Sprache im Kindes- und Erwachsenenalter verglichen werden. Erwachsene haben oft große Probleme, um einfache grammatische Regeln oder Vokabeln zu erlernen. Wogegen Kinder dies schnell in ihren Kopf abspeichern können. Genau dies gilt auch für den bewussten Umgang mit der Umwelt.
Wenn Menschen von vornherein lernen, dass sie bestimmte Arbeitsschritte oder Lebensweisen nachhaltig und umweltbewusst durchführen sollen, dann tun sie dies mit hoher Wahrscheinlichkeit für den Rest ihres Lebens. Dies gilt für Dinge wie Mülltrennung, richtiger Umgang mit Energien oder Konsumverhalten. Alles kann erlernt werden und sobald der Prozess verstanden und trainiert wurde, ist nachhaltige Produktion kinderleicht.